The brake disc that is half the weight and better for the environment
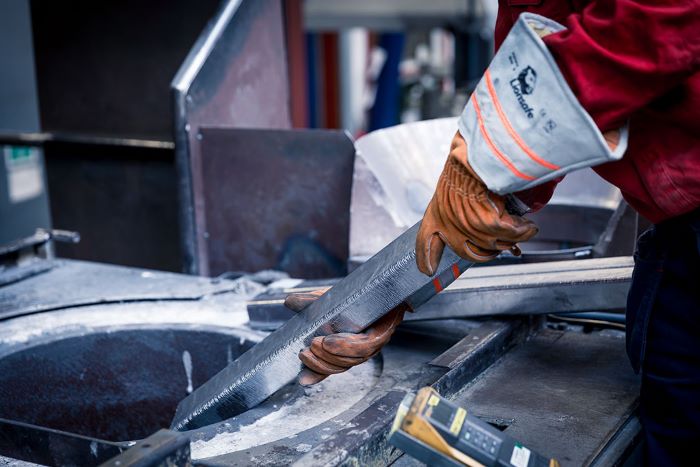
Imagine a brake disc that is 50 per cent lighter than today's and made from recycled aluminium. That's exactly what a new research project at Jönköping University (JU) has managed to create.
“By combining smart materials technology with a focus on sustainability, the vehicles of the future can be both lighter and greener,” says Lucia Lattanzi, Assistant Professor in Materials and Manufacturing - Casting, at Jönköping University School of Engineering (JTH) and project leader of the MaReAl project.
Lighter vehicles mean lower fuel consumption and less emissions, something that is crucial to reaching climate goals. At the same time, the need to extract new raw materials is reduced, saving both energy and natural resources.
“The result will have a major impact on society, as the brake discs can also be used for electric vehicles. Aluminium composites help to reduce the emissions from the discs when driving compared to using traditional cast iron and the recycled aluminium generates less CO2 emissions during production,” says Lucia Lattanzi.
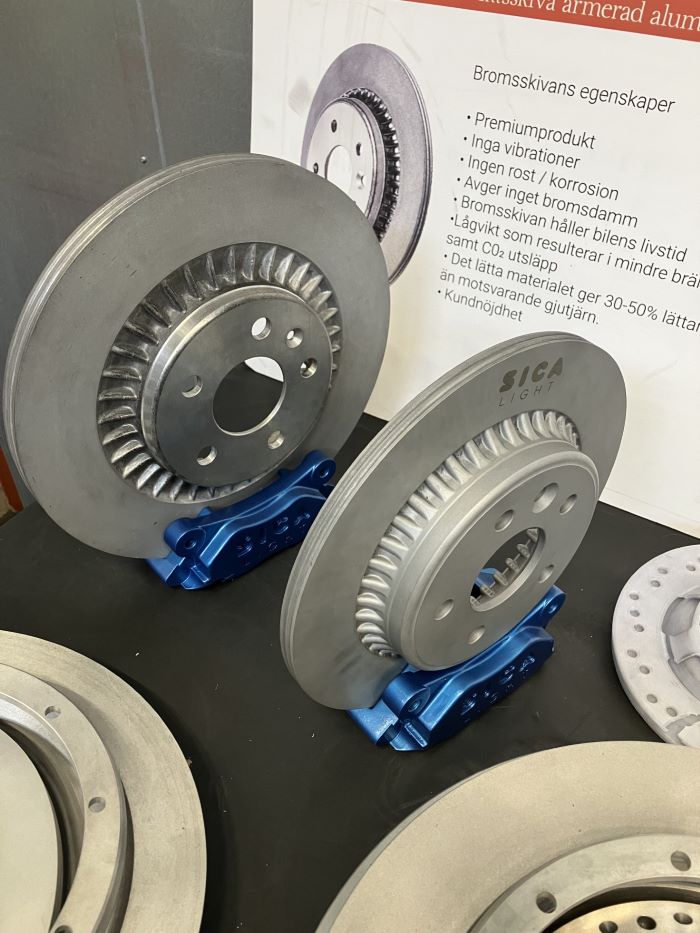
Lighter and more environmentally friendly brake discs
Heavy vehicle parts, such as brake discs, often use cast iron which is a heavy but durable material. In this project, the researchers are looking at a lighter alternative: aluminium-based composites. These are materials where aluminium is reinforced with hard particles, such as silicon carbide, to make it stronger and more durable. Mixing aluminium with hard particles also means that the material can withstand much more stress.
“What makes this project unique is the use of recycled aluminium alloys as a base. This not only makes the product lighter, but also more environmentally friendly,” says Lucia Lattanzi.
Lucia sees it as important to be able to contribute to a more sustainable development of the automotive industry. She thinks that the project is a successful example of good co-operation between universities, research institutes, and industry.
Samuel Awe is Head of Research and Senior Metallurgical Engineer at AC Floby, and he participated in the project together with RISE, Comptech and Gränges.
“This project has given us the opportunity to jointly address industrial challenges through applied research, knowledge sharing, and support. Through the project, we have been able to explore material friction and wear resistance, advanced alloy design, as well as processing in a collaborative environment, enriching both academic insights and industrial applications,” he says.
Samuel Awe also hopes that the project will lay the foundation for further collaboration leading to the development of lightweight, high-performance brake components with improved environmental and operational efficiency.
“I believe the project can also inspire further joint research projects and knowledge-sharing initiatives between academia and industry,” he says.
The automotive industry must reduce emissions
On 1 July 2025, the new Euro7 regulations governing emissions from cars in the EU will come into force. These will regulate, among other things, particulate matter (PM) emissions from brakes and tires.
“The new rules mean that the automotive industry will be forced to reduce PM emissions. This is where the new brake discs will really come in handy. Of course, my hope is that the industry will implement our results and that we will see this brake disc on cars in the future,” says Lucia Lattanzi.
Read more about the MaReAl project. External link, opens in new window.
What is an aluminium alloy?
An aluminium alloy is a material consisting of aluminium mixed with other metals to improve its properties, such as strength, corrosion resistance, thermal conductivity or formability.
What is a composite material?
A composite material is a mix of materials from different kinds of material categorys. The project focused on a metal matrix composite, where aluminium is reinforced by small ceramic particles.